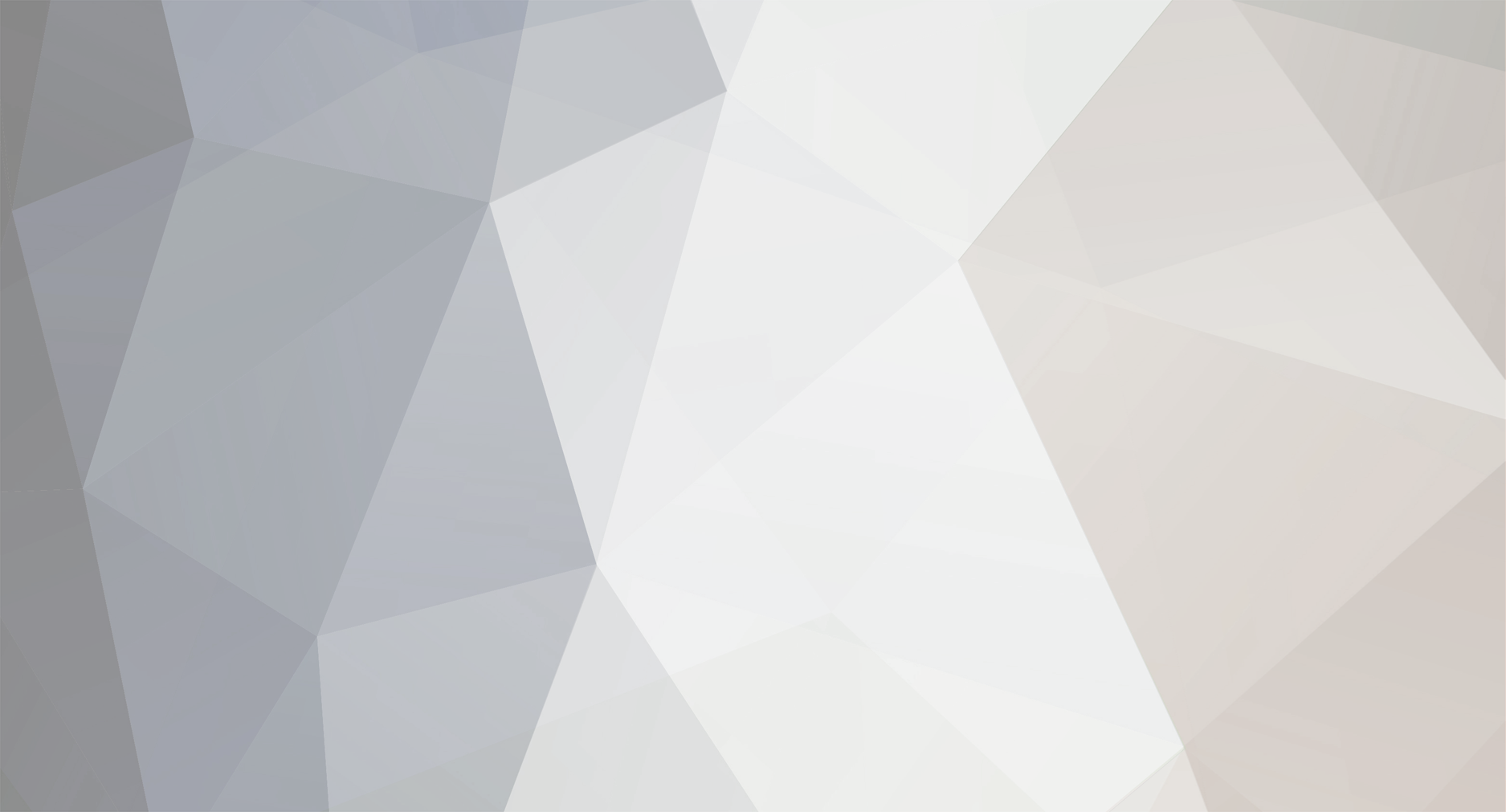
jasonm.
Expired Membership-
Posts
899 -
Joined
-
Last visited
Content Type
Profiles
Forums
Gallery
Events
Store
Everything posted by jasonm.
-
broken rings or chiped valve?
jasonm. replied to mmaleney's topic in Venture and Venture Royale Tech Talk ('83 - '93)
that valve may be too tight clearance..and likely burned too. pull valve cover, Check clearance -
Holes in air cleaner box
jasonm. replied to GigaWhiskey's topic in Venture and Venture Royale Tech Talk ('83 - '93)
there is a simple fix using my favorite DEVCON PLASTIC welder, from True Value hardware. 1st get some 1/8" plexyglass. Remove air box and filter. Sand the area around the holes. Cut the plexi to cover the holes. Sand the plexi too. Use the plastic welder per the instructions. You will not need much. I also use a popcicle stick to mix. Note: it sets in less than 5 min. sometimes, depends on air temp.. And fully hardened in less than 1 hours. As the carbs on these wear they run richer. And some did the "hole" thing to lean them out. -
Valve adjustment kit
jasonm. replied to hi-plainsdrifter's topic in Venture and Venture Royale Tech Talk ('83 - '93)
Curved tool will NOT work. Don't even think of it.- 21 replies
-
- contribute
- kit
-
(and 3 more)
Tagged with:
-
Steering Head Detented
jasonm. replied to GaryZ's topic in Venture and Venture Royale Tech Talk ('83 - '93)
No cuts needed if you have the correct tools. I used a hard faced piece of round steel 1/2" od. rod w/ 2lb. sledge. And there is just enough edge sticking out to get it out. Took no more than 5 hits. Maybe I have too many tools... -
85/83 boost sensor hook up
jasonm. replied to Venturous Randy's topic in Venture and Venture Royale Tech Talk ('83 - '93)
That's Odd. Then again, it's a Cali bike for sure w/ that emissions crap.. -
After market radiator cap
jasonm. replied to Venturous Randy's topic in Venture and Venture Royale Tech Talk ('83 - '93)
I got lucky finding a cap many years ago. I needed one and my truck looked like it had the same size. Well, holey crap it fit. My old Mitsubishi truck w/2.6 litre engine. cap Stant 227 -
it's a push-rod engine. V-4, 4 valve heads. I likey
-
Tank cover popping up on 1st gen help
jasonm. replied to dingy's topic in Venture and Venture Royale Tech Talk ('83 - '93)
maybe the 83 plastic is different. My 87 plastic is VERY stiff. And the front tab on mine engages completely. Cannot wiggle that cover for nutten. Although 2 times I pushed the front rubber grommey out of place. Now that will cause an issue. Plus the grommet has a right way and wrong for it to be installed. You take it out and you will see one side not like the other. tapered and wide vs. NOT. -
Steering Head Detented
jasonm. replied to GaryZ's topic in Venture and Venture Royale Tech Talk ('83 - '93)
Yes, they both wear out. I did mine 2 years ago. Unlike ball beariung types. These roller types. To the naked eye...you cannot see anything . Till you use a magnify-glass. And see lines where the bearings and races have made a microscopic dent. You remove the races. You cannot even feel the dents. The biggest reason they wear. 1st looseness...causes banging. And 2nd the lack of lube. Often due to water in the steering neck as I stated earlier. Lastly the wheel spends 99% of it's life pointed straight ahead, only moving a few degrees off center. -
What is this part in my oil pan?
jasonm. replied to dingy's topic in Venture and Venture Royale Tech Talk ('83 - '93)
obviously I would not use the toque wrench on something that I expect to be a major issue to loosen...like a car flywheel bolt. I guess we agree. simply , You cannot hurt a Torque wrench if the fastener is in the specified capable range of the wrench. -
Gasket list for 1st gen tear down
jasonm. replied to dingy's topic in Venture and Venture Royale Tech Talk ('83 - '93)
The guy I went to. Using the variable dyno...simulates how the bike responds on the road. Unlike a standard dyno which can only tell you full throttle info. Also the OEM head-pipes have ports to sniff each cylinder using the proper adaptor. This makes a big difference VS. a tail pipe sniffer. And is the only accurate way to set the low speed screw to perfection. You can make an adaptor. It's 6mm thread....- 6 replies
-
- gaskets
- gaskets transmission
-
(and 3 more)
Tagged with:
-
running hot
jasonm. replied to titansedriver's topic in Venture and Venture Royale Tech Talk ('83 - '93)
Titan, what was wrong with the housing...that you had to change it??? -
What is this part in my oil pan?
jasonm. replied to dingy's topic in Venture and Venture Royale Tech Talk ('83 - '93)
I don't think you are getting my point. you cannot wreck a torque wrench loosening a bolt that is torqued to 100 ft/lbs. If the wrench is rated at 150. Especially if you set the "clicker" much higher than the expected torque. I have used this wrench to both tighten and loosen lug nuts on my car for 20 years. I have had the calibration checked. None the worse for wear. -
Steering Head Detented
jasonm. replied to GaryZ's topic in Venture and Venture Royale Tech Talk ('83 - '93)
I do not know what this Vmax forum is trying to say. Heck....you drive out the old races. Make sure you did not put any dings in the seating area from your removal. Carefully drive the new races in using a BRASS punch or other soft material. I used a 4 oz. brass weight I have lying around. It is flat and I could carefully get the race in. Then you use the old race that you sanded the sides down to finish the job to fully seat the new race. The biggest hasssle is removing the lower bearing from the steering staft. Trick to this is to Hit only the bearing area you can see. And it won't be much as you start. Do NOT attempt to use a chisel or wedge...you will damage the lower tree. You could carefully use a dremal cutter wheel and cut it off. I have also done it this way. You cut thru almost all the way. Then your hammering the bearing off will crack the bearing enough to allow it to come off a bit easier sometime. I also suggest removing as much plastic as possible...windshield, etc. This will allow you to work from many angles while reinstalling the races. AND while you have it apart. Drill and tap the neck on the frame for a grease fitting. The neck will hold better than half a tube of grease. But you'll now be sure the bearings won't be dry and surely keep the water out. FYI, water comes down from the top because the top has NO seal. Justa metal cap. ALL THIS TAKES PATIENCE. Something I have in limited supply. SO what I am reporting here is 1st hand from my own successes and mistakes. -
Gasket list for 1st gen tear down
jasonm. replied to dingy's topic in Venture and Venture Royale Tech Talk ('83 - '93)
did you ever EGA the bike? Because a variable load type dyno and EGA will tell you absolutely how the engine is running. A 1mm difference in the carb size may net you some hp. But the EGA is always the way to start. Sounds like you have a lot of free time. The V-Boost set up can make a big difference. But again, the EGA is the ultimate tuning tool.- 6 replies
-
- gaskets
- gaskets transmission
-
(and 3 more)
Tagged with:
-
running hot
jasonm. replied to titansedriver's topic in Venture and Venture Royale Tech Talk ('83 - '93)
ALWAYS fill while on the side stand. Idle w/cap off. Keep topping up. Till the rad. is warm and the coolant starts to overflow the filler neck. Put cap on. AND make sure the remote reservoir is at the 1/2 full mark at least. Many forget about the remote reservoir on the right side in the fairing. -
My Luggage Rack Install
jasonm. replied to GaryZ's topic in Venture and Venture Royale Tech Talk ('83 - '93)
you want to spread the possible load out as much as possible. And "bonding " is the best way. So what ever is used should be glued or bonded to the inside of the trunk. Very often a washer does not spread the load enough because it bends. Thin steel strips 1/8" or 1/16" are bendable and can be bonded using my farorite Devcon Plastic Welder. Then what ever reinforcement you make, use the glue. Put the bolts in and tighten to clamp it all down. If you are afraid of the glue on the bolts. Put a bit of WD40 on them before assembly. -
What is this part in my oil pan?
jasonm. replied to dingy's topic in Venture and Venture Royale Tech Talk ('83 - '93)
My wrench is rated for 150 ft/lbs. and the bolt is rated far less. It's long like a breaker bar. Plus I did not have a breaker bar at the time. Using a torque wrench to loosen something is not going to do any harm. That's why they click both directions. -
Different clutch issue
jasonm. replied to Marcarl's topic in Venture and Venture Royale Tech Talk ('83 - '93)
if the bushing is worn...you will not disengage the clutch. His problem sounds like the opposite. ALL masters have a bleed return hole. It's very very small. If it's plugged...it can cause the symptoms described. Removing the master and blowing it out w/compressed air and some cleaner...could do the trick. Also you may see the hole once you remove the filler cap.And a small 26 awg wire or smaller may clear it out. ... I JUST REMEMBERED. I had this same issue. 10 + years ago. The cause was the clutch hose had internally failed. But not leaked a bit. The pull was very stiff and it did not engage till the end. NOTE: the hose makes a very sharp bend at the steering neck . And that is the failure area. I actually could faintly hear the hose burp and shake as I pulled the lever. Because the hose had internally broken...the fluid was being blocked from flow. Because it was just before a trip. I ordered an original hose. Then 2 year later changed to SS hose and fittings. So I have a spare should someone need one. My SS hose I thnk is 63". But recommend a bit longer. 64 or 65. I suggest you measure if you upgrade to SS. You need a straight banjo at the slave and a 35 and the master. -
exhaust leak
jasonm. replied to Dr. Psycho's topic in Venture and Venture Royale Tech Talk ('83 - '93)
Yes, #16 copper ring. Then you have the Clamp rings on each side which squeeze it using the ODD looking stainless clamp. My Vision uses the same design. YOU MUST SLIDE THE rear HEADER PIPE AWAY FROM THE HEAD to do all this. Usually you have to disassemble the whole exhaust system because these copper rings at the rear head and clamps are the 1st things installed at the factory. 2nd- the chamber under the engine then front head pipes. Taking a short cut usually results in a future leak. The trick here. Slide 1 clamp ring then copper ring then the 2nd clamp ring. Push the pipe back into the to the head.Then carefully spread the CLAMP over the assembly. Basically you are making a sandwich. bread meat bread. But now it's clamping ring, copper ring , clamping ring. All squeezed together with the special clamp. Not you cannot do one side w/o doing the other. So you tighten both clamps last at the same time. If you want a picture of the parts as they should look...email me. I have spares from my vision lying around. Which are same but slightly smaller. -
Trying To Fill Differential
jasonm. replied to GaryZ's topic in Venture and Venture Royale Tech Talk ('83 - '93)
I know the 1300 has a sealing washer. So there is no need to wrap the threads on a 1300. I thought the 1200 also had the same waher? Using teflon tape only invites bits of the tape to fall into the rear drive when you remove the plug...next time. So I cannot understand why you would do that....A bit of high temp grease on the threads makes more sense to me. Not to mention the oil that is on the threads from the last change. I just think it's an issue for those who do not change the rear oil often enough.- 9 replies
-
- allen
- differential
-
(and 3 more)
Tagged with:
-
Ideas to fix this oil leak
jasonm. replied to mlew's topic in Venture and Venture Royale Tech Talk ('83 - '93)
Yes, I also used my brake vacuum bleeder w/small hose when I had the same issue. I used Permatex ULTRA GREY. which any excess blended into the stock head color just fine. No leaks since the work 2k ago. -
exhaust leak
jasonm. replied to Dr. Psycho's topic in Venture and Venture Royale Tech Talk ('83 - '93)
Did they hand you COPPER rings. If not...you got the wrong part. They may have handed you the gasket for the head. The copper goes between the " steel sandwich rings". Nothing can fall out. -
Individual K&N Filters
jasonm. replied to MikeZ06Allen's topic in Venture and Venture Royale Tech Talk ('83 - '93)
Mike, many hear believe they have made performance improvements. But gas mileage obviously will suffer with what you are considering. BUT you should do ONE thing after you think you have things good. Find a Dyno shop with an variable load capable dyno and EGA machine. This can confirm if you you are way rich or lean.Properly tuned bike can often have almost as good mileage while cruising unless you flog it hard. If you keep OEM YAmaha head pipes...there are plugs(6mm thread bolt) on each..made for the proper adapter to shiff the cylinder's indiviually. I made my own. I have had my bike 20+ years. I did this last year -EGA . This is the best it has run...with today's crap gas. You basiclly want the A/F ratio 13:1 up to 13.5:1 or also known as 1.5- 2.0% CO. As this gives best power. And don't forget to set the EGA at idle also. Mine was set 5th gear run with "25% load" and the EGA read 13.5 @ 4500 - 5000rpm cruise, not full throttle. This is where needle shimming comes in. So to put it simply it's not a "fast and easy" process. May take more than one trip to the dyno room. Especially when you have to rejet. And depending on where you go the prices vary. But once it's done...IT'S DONE! Tip- find a dyno guy who hates Harleys...and has much patience. They tend to be very informative and know 4 cylinder machines. Lastly if my bike could keep 13:1 all the way to redline during full throttle it would have hit 100hp. Yes it's stock w/airbox K&N. But the carbs a worn and she runs rich(12:1) during full throttle. -
What is this part in my oil pan?
jasonm. replied to dingy's topic in Venture and Venture Royale Tech Talk ('83 - '93)
seems like the manual is what is to be followed. It clearly shows using a 32mm open end wrench on the flywheel when removing the flywheel bolt. Mine came out easliy with my 1/2" torque wrench. Sorry to see your problems. FYI, when changing the crank..you MUST use the chart regarding the #'s printed on the crank and elsewhere to use the right sized main bearings...you now need to read the OEM manual.