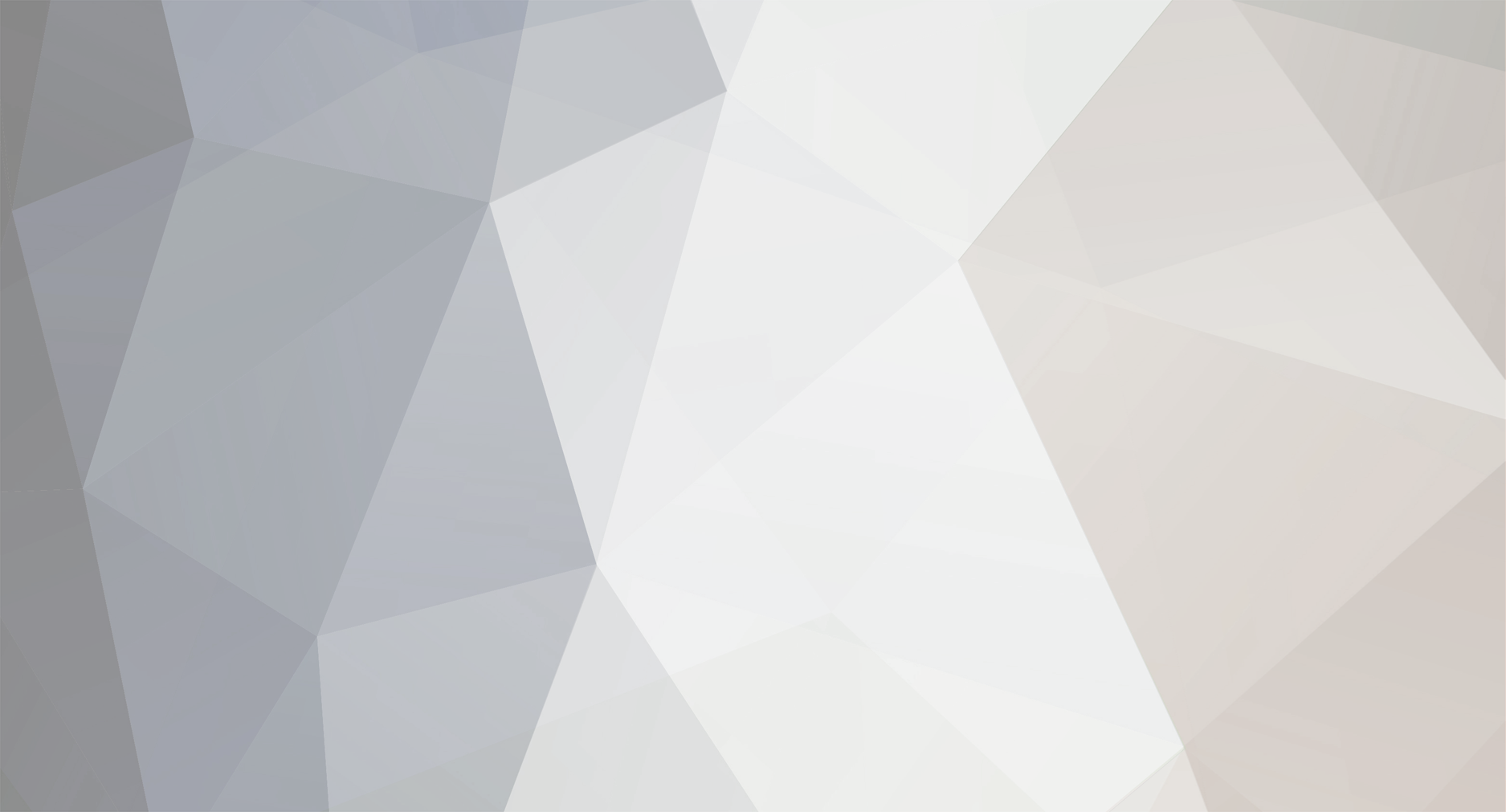
windrider1983
Supporting Member-
Posts
36 -
Joined
-
Last visited
Content Type
Profiles
Forums
Gallery
Events
Store
Everything posted by windrider1983
-
Rear brake caliber dragging
windrider1983 replied to SpencerPJ's topic in Venture and Venture Royale Tech Talk ('83 - '93)
This was all good info - I had seen other posts on the MC rebuild a few years ago but couldn't find them, so this was quite helpful (I also had a rear brake lockup recently). Thanks to Squidley for the conversation also. I was wondering if anyone knew why there was not a diagram that showed the parts inside the proportioning valve portion of the MC? And if there is a rebuild kit for it? I was able to clean mine up - the rubber boot on the copper piece still seems good, as well as the o-ring on the big 19mm cap bolt. What if those were rotted or if the spring was too rusty to clean up? Or has everyone been lucky and not needed to replace any of these? Or have they just scrapped it at that point and split the rear from the front brake and eliminated the part altogether? Just curious... -
One would think that after owning this bike for 27 years, I would instinctively know the most basic of the safety features - but give Larrydr a cupie doll - the kickstand WAS down and that was why it was shutting down when I was putting it in gear in the garage on the big stand (duh). The transmission seems fine now that I can put it in gear. But the brake is definitely hanging up - so the first and simplest diagnosis was the correct one - stuck brake. So now I just need to pull it apart and determine why. I replaced everything but the piston on the brake about 4 years ago but have not put a lot of miles on it since then (and all local travel) - and it has only been out twice this year until I got the speedo lubed up. The comment about the washer on the wrong spot on the rear axle makes me curious, though I thought I was pretty careful to put everything back the way I found it when i had the wheel off. Thanks for all the thought you folks put into this and the suggestions. Certainly a big relief that the transmission is not the culprit.
-
I was road testing the lubricating of the odometer yesterday evening (used the info in an earlier thread about making a zerc fitting - seems to have worked) - so the odometer whine was gone - was happy about that. But while cruising up the freeway at 70 mph, enjoying the silence, the bike suddenly starting lugging and losing speed, dropping to 50 almost before I could tell what was going on. At that point I tried to downshift and as soon as I pulled in the clutch it seemed like the rear wheel locked up (screeching and tire smoke). I was in the process of downshifting to 4th so I continued that, popping the clutch and it seemed to at least get the wheel moving again but continued to struggle. At this point I was in the left lane in traffic trying to get over and out of the moving lanes and fortunately caught a brief break in the flow and got to the berm - when i pulled the clutch again, the rear wheel again locked up. I somehow worked the gears and the clutch enough to get to a very quick but controlled stop and the engine stopped at the same time as the bike. It would start and idle normally, and rev normally, but dropping it into first or second immediately caused it to stall (instantaneously). Needless to say, called AAA and I was back in my garage about 2 hours later. Is this definitely a transmission issue, or possible final gear in the rear hub (it did seem stuck initially when we went to roll it up on the tow truck ramp, but it did start rolling then), or something else? Not sure where to start.
-
Final (I hope) conclusion to this thread - everything is back together, it started relatively easily and runs great. Flushed both the oil and coolant systems with new fluids and oil filter, then drained both and filled with new again (and another new filter). Shortly thereafter, we had a break in the Ohio weather and I took it out for the first time in nearly a year and it felt good. The rear brake needs adjusted badly (or it has air in it) so that needs some attention, but NO LEAKS anywhere that I can see. Thanks to everyone who provided assistance and advice.
-
I asked that same question early in this thread, and was told yes. Having removed it with the carbs off, I can't say for certain that it couldn't be done with them on, but it would be difficult. You would have to disconnect the steel oil lines (with the banjo fittings) from the cylinder heads, and be able to crack loose the 6 bolts holding the asembly to the crankcase. Those came loose fairly easily with a socket wrench working from above (with plenty of room for applying leverage), but not sure you could get a good byte on them coming in from the side. Another tricky part would be setting the unit back in place and keeping the new gaskets properly aligned. If that is not right, then you are back to square one. Having done it the 'easy' way (pulling the box and carbs), I might try to get it loose first and see how far I could get, but be prepared to fall back to the original procedure.
-
Surprisingly, I found no problems with the carb boots and the diaphrams were all good, so we decided to put it back together today. We reinstalled the distribution module with the new gaskets, and then reinstalled the carb assembly. After attaching the throttle cables, we noticed that the throttle was no longer returning freely - sticks especially after twisting it wide open. We cannot see where we have anything connected wrong. Is it possible we stretched one of the cables and it needs adjusted? Or other likely suspects? I have not found an adjustment procedure in the manual, but still looking. Addendum before anyone had a chance to respond - on a hunch we unclamped the carbs, pulled them loose, and reseated them without clamping - and the sticking throttle was gone. Seemed like something was applying a small warp to the linkage and causing it to hang up a bit. After reclamping the boots one at at time and checking the throttle in between each, we got it to an acceptable point. Airbox is back on, though I am missing a spring clamp to complete the install of the service bulletin noted above (bought the ones noted in the bulletin, but did not realize one of the originals was missing) - will try to find one tomorrow.
-
Thanks for all the info - it is as Prairehammer indicated - the update to the breather box and drain tube was never done on my 83. I have ordered the parts needed - the updated breather hose, the t-fitting, some clips. I will re-use the small drain line as indicated in the bulletin - it is still pretty flexible, even after 37 years. And I will seal the boots, as stated in the bulletin. After that - take a look at the carbs. Thanks again!
-
I started working on the twinkie today - got the carbs out, removed and cleaned up the twinkie, and now have a few questions. 1. The Crankcase breather tube is bad and needs replaced. Cannot find a diagram with that part on it. It appears to be a formed hose but not sure. 2. The tube coming out of the crankcase housing that feeds the pressurized oil fitting has an o-ring on it. It looks OK, but would make sense to replace it if I knew what size it was or the part #. 3. When I reassemble the twinkie with the new gaskets, is it appropriate to coat them lightly with a gasket sealer, or best to leave them as is? Thanks for any info or opinions.
-
Thanks for the info - that is exactly what I needed to know. And while the coolant does not appear to be contaminated, the oil most certainly has to be - the level is completely above the view window - which it was not when I put it up for the winter. So I have drained the coolant (so it doesn't leak anymore into the lube system), drained the oil, and put a piece of tape over the ignition. I haven't planned when I will start the project yet - is there any harm in letting it sit for a while in the present condition? Once the gaskets are replaced, should the engine be flushed to remove any residual coolant from the lubrication system? Sacrifice 4 quarts of oil and a filter - run it for a few minutes and then drain it all out? I am thinking it may be an opportunity to rebuild the carbs as well, but have not looked at the cost of the rebuild kits yet, or everything that is involved with that. It currently runs pretty well, so probably not absolutely necessary, but with 85K they are probably due. I have decided to purchase Big Auggie's 89 Royale so I can still get some riding in this season (plus it is a good upgrade from the 83), and I may have a buddy interested in the 83 once it is running again. Appreciate all the info provided so far (and I am impressed by the Google Drive link, btw). Mark.
-
I have an 83 Venture(stock, not a Royale), and I have a small coolant leak. It has been very minor and originally only would be noticeable over the winter - I would keep an oil pan under the bike with a couple of paper towels and they would be damp by spring. Last summer it started to leave a drop or two overnight - that is when I started looking. BTW - I had rebuilt the water pump and replaced all the hoses a couple of years ago, so it is not the water pump or related O-rings or fittings. Over this past winter, it was worse – I lost what was in the overflow reservoir plus a little more. It appears to be coming from the front side of the crankcase breather box (I assume that is what that cigar-shaped assembly that sits between the cylinders is). Over a period of several days, the small hollow depression on the front side of the block, visible from the left side, will slowly accumulate green antifreeze (only when the bike is sitting on the big stand. When leaning on the kickstand, it runs down the left side, one drop at a time). I have checked all the lines coming out the top of that box and none have any residue or liquid at the fittings or clamps. The only conclusion I have been able to come to is one of the two gaskets leaks when it cools off. If it leaks when it's hot, it is so slow that it is burning off before you can see it. Does anyone have any experience with this? Can the bolts be retorqued? If so, what is the correct torque (haven't been able to find it in the manual). What would be involved in replacing the gaskets? Can it even be done without removing the carbs, or more? Besides the couple of hose fittings, there is a banjo fitting with two chrome tubes running to the front and back cylinder housings - I assume those are coolant lines, but not sure - is there a write-up on this site that explains what each of these lines are for? I just like to understand what I'm looking at. I did put a small socket on the bolts on the left side to see if there was any play in them, without putting too much effort into it – I fear snapping one of them off and having a real mess – but they wouldn’t budge. Since it seems to be worse when it gets cold, I even tried setting a ziplock bag of ice on the top of the assembly and after half an hour or so later, tried to tighten the bolts on the left side again. The bolt closest to the outside edge did budge just a tiny bit, but the two in the middle still did not move with the pressure I was using. The first picture shows the well about half full of coolant, and the second shows a bit of coolant just under that bolt housing to the left of the well. Thoughts?
-
Glad it helped. Hopefully you will get many miles of trouble-free cooling out of it.
- 3 replies
-
- coolant drip
- coolant leak
-
(and 3 more)
Tagged with:
-
I was searching for info on first gen side panel vents and didn't see any recent posts. My right side melted recently when it came partially detached from the panel and tilted inward when I parked it - got too close to the cylinder head and most of the louvers melted, along with the rail they plug in to, and the turn wheel. Very sad, because it was in great shape (except the tabs were all in various degrees of broken and repaired, which is why it came loose). Does anyone have a new or used one they would be willing to sell? Thanks, Mark Miller (Windrider1983)
-
Thanks to all for their comments. I did pull the cable and sleeve. The sleeve and cable looked wet, but I blew the sleeve out with brake cleaner and let it hang for a while. I was able to squirt some lithium lube up into the speedometer fitting. I did the same with the sleeve and reassembled it all. Took it out for a test ride and the howl kicked in about 60 MPH, but quit after about 30 seconds and never returned that afternoon. Of course it was in the afternoon and warm. I rode it to work the next morning when it was cooler, and it did start again as I hit the freeway, but again it quit after about 30 seconds. I have not been out since then, but will see what happens. If i can put a couple hours together, I will pull the instrument cluster see if i can do a better job of getting the lube into the bearing. Seems like the next step, unless someone has one of those fittings they are willing to part with. But now that I know what it is, I am not concerned about riding it. Still got a month or two if Ohio weather cooperates. Thanks again. Mark.
-
Thanks to all for the comments - I guess I am relieved that it's probably not anything too serious. I will try pulling the cable and see if that eliminates it. I have had the instrument panel completely off, recently to re-solder the computer module, and before that to replace all those bulbs. What is the best lube for the cable, and is it the same as what you use to lube the speedo gear? I watched the video from Bluesky but didn't catch what he used on the cable -said he used Yamalube Racing grease (lithium based) for the gear. So if the speedo does go bad, am I looking at replacing it with a salvage one, or are new units available? Come to think of it, I do have an entire instrument cluster from an 86 I believe (came with something else i bought a few years back - buried in the crawlspace with other miscellaneous parts). I am assuming that the entire cluster is not compatible, but the speedometer itself probably is? It will probably be later this week, or the weekend, before I can try anything, but will post back with any results. Thanks again everyone.
-
To preface this question, I have done a number of maintenance items on my stock 83 Venture over the last year, and just recently got it back on the road. Here is the list of what I have completed: [TABLE=width: 527] [TR] [TD=colspan: 2]Repairs/Maintenance beginning Summer 2016 thru July 2017[/TD] [/TR] [TR] [TD]1[/TD] [TD] re-solder computer module to main circuit board[/TD] [/TR] [TR] [TD]2[/TD] [TD] Replace rear wheel bearings[/TD] [/TR] [TR] [TD]3[/TD] [TD] Change final gear oil, clean and lub drive shaft[/TD] [/TR] [TR] [TD]4[/TD] [TD] Replace spark plugs and wires[/TD] [/TR] [TR] [TD]5[/TD] [TD] Replace all coolant hoses (7) - these were the original hoses[/TD] [/TR] [TR] [TD]6[/TD] [TD] Rebuild water pump[/TD] [/TR] [TR] [TD]7[/TD] [TD] Flush and refill antifreeze[/TD] [/TR] [TR] [TD]8[/TD] [TD] Replace all brake lines and hydraulic clutch line with braided stainless steel lines[/TD] [/TR] [TR] [TD]9[/TD] [TD] Clean calipers and replace all brake pads[/TD] [/TR] [/TABLE] To do all that, I had the entire faring off the bike, saddlebags and tailpiece – pretty much everything except the trunk (only the second time I have done that – the first when my brother-in-law repainted it). But anyway, I finally got it all back together in late July. The bike is largely a hobby for me, and I typically ride it to work during the good weather here in Ohio. So the first week or so went fine. Then I noticed a new sound one morning, and it has recurred on multiple occasions. It doesn’t kick in until I have been cruising about 60 or 70 mph and then suddenly I hear a significant whine coming from the front of the bike. It is a fairly high frequency but not ear piercing, and definitely loud enough you immediately hear it and know its not normal – like something is vibrating quite fast and sounds like metal. It remains at a constant pitch and intensity regardless of engine RPMs or whether I shift or disengage the transmission, or brake, or anything else I have tried to do to figure out what it is. The one consistent thing is that it doesn’t start until I have exceeded 60 MPH, and it magically quits when my speed drops to about 30 MPH. At first I suspected the cooling fan, but the noise seems to start before the point when the fan normally kicks in. The fan is working the same as it has in the past in that it starts when the needle is almost touching the red . Of course I can’t hear it when cruising, but it often comes on when sitting at a traffic light or when I pull it into the garage just before shutting it off – so it is running as it always has. I searched the forums for some clues, and did find a post about a spot weld on the fan cowling coming loose and allowing the fan blades to start rubbing. So this past weekend I pulled the radiator cover off (and the associated side panels) and took a look at the cowling – everything seemed tight and locked down, at least what I could reach with a long screwdriver to pry it a bit to see if anything seemed loose. The fan blades spun smoothly – just could not see anything that was out of place. So without putting the covers back on, I took it out for a run up the freeway about 10 miles, running around 70, with a short stretch at 80, and no noise. This was late Saturday morning with the ambient temperature in the low 80s, so it was plenty hot the whole trip. So I wondered if one of the covers was just not on properly and was vibrating at high speeds. So back home I let it sit and watched some football, then put the radiator cover and side panels back on, taking care that everything went where it belonged and fit snugly. I noticed that the turn signal module that is loosely zip tied to the frame under the faring was a little sloppy, so I tucked it back up out of the way a little further with some packing material, just in case it was doing some weird vibrating thing (though I could not imagine it making that much noise, even at 80). I then took it out again and repeated the trip – it was even warmer then, but still no mysterious noise (and I could hear the fan cycle on when I stopped at the end of the off-ramp waiting for the traffic light to change). So I got back home with no conclusive evidence that I had solved anything, but hoped I might have. So I rode it to work this morning – about 7am – reasonably cool out (mid-60’s), and I was no more than two miles on the outerbelt when the noise kicked in again (around 65 MPH). The temperature gauge was still below where the fan normally kicks in, so it really does not seem to be that, at least not when the fan is running. I encountered some traffic as I continued toward downtown, and as I slowed below 30, it quit. I did have it up to about 60 once more for a short time but the noise did not come back. On the ride home this afternoon, plenty hot, and had it moving a few times near 70 or maybe a little above – no noise. So I am out of ideas. Any thoughts or suggestions, or links to other possibly related posts would be greatly appreciated.
-
I did use a socket, but got a suggestion from a neighbor on using a bolt to draw it down, rather than the hammer method. I documented what i did and posted it to a new post with some attachments. Link to the YouTube video has been added - here is the link to the other post: http://www.venturerider.org/forum/showthread.php?129023-Water-Pump-rebuild-narrative-and-video
-
1983 Yamaha Venture – Water Pump Rebuild During the process of replacing all of the coolant hoses on the 83Venture, I noticed that I was getting a fairly consistent amount of coolant spurtingout of the weep hole in the water pump housing. It had been doing a littledripping the last couple of seasons, but not enough to prompt me to do anythingabout it. But after replacing all of the hoses and flushing the system a coupleof times with water, followed by a refill with fresh antifreeze, the minor dripturned into a steady pulsating leak. So that precipitated the decision torebuild the whole pump. I purchased a complete rebuild kit from Buckeye Performance(Cincinnati). This included a new impeller (mine still had the original plasticone), and I also requested that it include the L-Joint Tube (and o-rings) thatconnect to the thermostat housing, as mine had a ding right in the elbow and Ithought it best to just replace it now while it was easy. Those two parts werethe most expensive contributors to the over $200 price tag of the kit. If youonly need the seals, bearing, and gaskets/o-rings, you could probably get awaywith less than $100. After removing the pump from the bike, I cleaned off all the old gasketmaterial from both the pump and the bike. There was also some minor effects ofcorrosion in a few spots that I was able to minimize with some wadding polish.I then disassembled the pump, basically foyoutube link for videollowing the manual – though theinstructions for removing the mechanical seal was not detailed enough for theinexperienced (me). It has to be hammered out (the book say “tapping”, but Iwould define it as ‘hammering’) from the bearing side. Since I was replacingall of those parts, I pulled out the oil seal through the bearing first, makingsufficient room to hit the mechanical seal with a small drift pin and hammer itout. Then an easy matter to flip the assembly over and hammer out the bearing. Iam not sure how you would do it if you just wanted to replace the mechanicalseals. Having it apart, I began to understand how it all was designed to work,and in particular, why that weep hole is there. The weep hole is a channel thatruns through the outside of the housing to an inner air space that is inbetween the oil seal (on the oil-side of the pump) and the mechanical seal (onthe coolant side of the pump). This is a safety valve of sorts, so if any oilgets past the oil seal, or any coolant gets past the mechanical seal, itescapes out the weep hole, rather than potentially invading the opposite sideand contaminating the oil or coolant. The oil seal is a fairly traditionalrubber seal that sits next to the bearing and the impeller shaft just slipsthrough it. The mechanical seal, which is meant to prevent the coolant fromslipping past the shaft of the impeller, is actually two pieces – one thatinstalls over the impeller shaft and seats in the impeller body, and the otheris a spring-loaded piece that is pressed into the pump housing on the coolantside. Both pieces have a smooth surface that the book calls ‘ceramic’, andthese mate to each other once the impeller is installed back into the housing.The impeller obviously spins while the piece pressed into the housing remainsstationary. The smooth surfaces are meant to allow that motion to occur whilepreventing any coolant from leaking down the shaft toward the oil side of thepump. If any does, it hits the air space and exits via the weep hole mentionedabove. The spring in the mechanical seal is designed to continually applypressure so that the two smooth surfaces maintain constant contact. That mayhave something to do with the temperature variations, or just a way to ensurethat it maintains a tight fit after assembly. I am guessing that the reason wesee leakage in these old bikes is that the springs start losing some of theirtension, or the smooth surfaces just get worn and start allowing leakage, perhapsonly at certain temperatures. So much for the analytical stuff. The installation of the seals and bearing was no more detailed in themanual than the disassembly, other than it mentioned a ‘special tool’ forpressing in the mechanical seal. You could tell from the picture that this toolwas meant to apply pressure on the outer lip of the mechanical seal (to avoidputting any pressure on the spring loaded ceramic surface in the inner portionof the seal). I had read in one of the forums that someone had used a largesocket that sat on the lip of the seal and allowed the inner portion to pass upinto the body of the socket. That forum entry did not provide any details onhow to utilize that tool to then press the seal into the housing, and therewere a couple of entries in other posts of folks damaging the seal in theprocess of trying to hammer it in place (it is light aluminum and will distorteasily, rendering it useless). I investigated the possibility of using a smallarbor press, and after exhausting my list of contacts and neighbors, I actuallybought a cheap one from Harbor Freight. But in the process of borrowing anappropriate socket from my neighbor (a 1&1/16 impact driver socket fitperfectly), he sized it up for about 10 seconds and then said ‘you could run abolt up through the housing and probably just draw it down with a socket andwrench – just need a bolt, a couple of big washers, and a nut”.Simple and brilliant (I returned the arborpress at that point).I mounted the pumphousing on a board, after drilling a couple of holes to match the housing boltpattern, and one that lined up with the opening for the seals. I purchased a 6inch hex-head bolt (5/16th inch diameter I think) and some washersand corresponding nut. The book also calls for using Yamabond #4 as anadditional sealant on the inner surface of the housing, so I did pick up a tubeof that from the local bike shop. This is applied on the inner surface of thehousing just prior to installation of the seal. It says to use a small amount,and you also want to be careful not to plug the weep hole. It also says toapply a small amount of grease to the lip of the seal – not sure what purposethis serves, but I did as instructed.Ithen ran the bolt up through the board and the center of the pump assembly,then thought better of having threads that close to the inner wall of thehousing where the oil seal sits, so I pulled it out and put some electricaltape on that part of the threads just to make sure I did not inadvertentlyscratch the housing there. I then sat the seal in place on the housing, thesocket on top of the seal, a couple of washers and the nut and snugged it up,trying to keep the seal as straight as possible on the housing. You can’t seemuch of it at this point, but enough to make sure it is straight on. Then justa matter of slowly tightening it up – watching as it goes – but once it startsyou are pretty much committed. You will know when it is fully seated and can’tbe tightened any more. I did discover after removing the bolt and socket, thatone side had just a slight gap (enough to feel with a finger nail), so Ireinstalled the apparatus and retightened, then loosened and rotated the socketa bit and retightened, repeating this procedure until I had rotated the socketa full 360 degrees.This took care ofthe gap. At this point, visually verify that the weep hole is still clear –clean it out with a pick or maybe a pipe cleaner if necessary. The second piece of the mechanical seal is the rubber/ceramic seal thatgoes in the body of the impeller. If you are reusing the impeller, you need to removethe old seal and replace it with the new one – simply apply a little coolant tothe new seal to help lubricate it and slide it down the shaft into the body ofthe impeller. The manual says to measure that the seal fits squarely inrelation to the shaft (no tilt) – I just slipped it into place and pressed itin with my fingers - it seemed flat and flush, so hoping there is nothing moreto it than that. The next step is to install the oil seal and then the bearing. The oilseal just slips in (printed side down). The bearing needs pressed in next. Iconsidered using a narrower gauge bolt and repeating the above procedure fromthe opposite side to press in the bearing, but I was worried about the boltdamaging the inner surface of the oil seal, which the spinning shaft of theimpeller runs against. If you used a partially threaded bolt, the press methodwould probably be fine. But the bearing, being made of high quality steel, canwithstand some light hammering, so I went that route – putting a little oil onthe new bearing as a lubricant, then using the old bearing on top of the newone, with a large washer over the old bearing, and the impact socket on top ofthe washer as my hammering point. Tapping in a circular pattern around thesocket until it began to go in and just continuing until it felt seated. Itdoes not go in completely flush with the housing, but sticks out just a bit.You will know when you insert the impeller through from the other side – if theindentation for the circlip is not exposed, then the bearing is not fullyseated. At this point it is a simple matter to lube the shaft of the impellerand insert it thru the seals, install the circlip, install the dowel pin,install the gear, and the final circlip. You are now ready to install the pump back on the bike.I was replacing the L-Joint tube thatconnects to the thermostat housing, so I had a new one of those and newo-rings. If you are using the old tube, you probably at least want to replacethose o-rings. Then mount the housing back on the bike with the new gasket,then the outer housing with the new o-ring, tightening everything to spec (7.2ft/lb). Don’t forget to fill it with antifreeze before starting the bike! I have included attachments - a word doc that includes the above, and a diagram/parts list. The video that shows the assembly of the seals and bearing can be found on YouTube at this link: Hope this is some help to anyone still working on these bikes. Water-Pump-83-Venture-rebuild-narrative.docx Water-Pump-diagram-83-Venture-with-notes.pdf
-
1983 Yamaha Venture – Water Pump Rebuild During the process of replacing all of the coolant hoses on the 83Venture, I noticed that I was getting a fairly consistent amount of coolant spurtingout of the weep hole in the water pump housing. It had been doing a littledripping the last couple of seasons, but not enough to prompt me to do anythingabout it. But after replacing all of the hoses and flushing the system a coupleof times with water, followed by a refill with fresh antifreeze, the minor dripturned into a steady pulsating leak. So that precipitated the decision torebuild the whole pump. I purchased a complete rebuild kit from Buckeye Performance(Cincinnati). This included a new impeller (mine still had the original plasticone), and I also requested that it include the L-Joint Tube (and o-rings) thatconnect to the thermostat housing, as mine had a ding right in the elbow and Ithought it best to just replace it now while it was easy. Those two parts werethe most expensive contributors to the over $200 price tag of the kit. If youonly need the seals, bearing, and gaskets/o-rings, you could probably get awaywith less than $100. After removing the pump from the bike, I cleaned off all the old gasketmaterial from both the pump and the bike. There was also some minor effects ofcorrosion in a few spots that I was able to minimize with some wadding polish.I then disassembled the pump, basically foyoutube link for videollowing the manual – though theinstructions for removing the mechanical seal was not detailed enough for theinexperienced (me). It has to be hammered out (the book say “tapping”, but Iwould define it as ‘hammering’) from the bearing side. Since I was replacingall of those parts, I pulled out the oil seal through the bearing first, makingsufficient room to hit the mechanical seal with a small drift pin and hammer itout. Then an easy matter to flip the assembly over and hammer out the bearing. Iam not sure how you would do it if you just wanted to replace the mechanicalseals. Having it apart, I began to understand how it all was designed to work,and in particular, why that weep hole is there. The weep hole is a channel thatruns through the outside of the housing to an inner air space that is inbetween the oil seal (on the oil-side of the pump) and the mechanical seal (onthe coolant side of the pump). This is a safety valve of sorts, so if any oilgets past the oil seal, or any coolant gets past the mechanical seal, itescapes out the weep hole, rather than potentially invading the opposite sideand contaminating the oil or coolant. The oil seal is a fairly traditionalrubber seal that sits next to the bearing and the impeller shaft just slipsthrough it. The mechanical seal, which is meant to prevent the coolant fromslipping past the shaft of the impeller, is actually two pieces – one thatinstalls over the impeller shaft and seats in the impeller body, and the otheris a spring-loaded piece that is pressed into the pump housing on the coolantside. Both pieces have a smooth surface that the book calls ‘ceramic’, andthese mate to each other once the impeller is installed back into the housing.The impeller obviously spins while the piece pressed into the housing remainsstationary. The smooth surfaces are meant to allow that motion to occur whilepreventing any coolant from leaking down the shaft toward the oil side of thepump. If any does, it hits the air space and exits via the weep hole mentionedabove. The spring in the mechanical seal is designed to continually applypressure so that the two smooth surfaces maintain constant contact. That mayhave something to do with the temperature variations, or just a way to ensurethat it maintains a tight fit after assembly. I am guessing that the reason wesee leakage in these old bikes is that the springs start losing some of theirtension, or the smooth surfaces just get worn and start allowing leakage, perhapsonly at certain temperatures. So much for the analytical stuff. The installation of the seals and bearing was no more detailed in themanual than the disassembly, other than it mentioned a ‘special tool’ forpressing in the mechanical seal. You could tell from the picture that this toolwas meant to apply pressure on the outer lip of the mechanical seal (to avoidputting any pressure on the spring loaded ceramic surface in the inner portionof the seal). I had read in one of the forums that someone had used a largesocket that sat on the lip of the seal and allowed the inner portion to pass upinto the body of the socket. That forum entry did not provide any details onhow to utilize that tool to then press the seal into the housing, and therewere a couple of entries in other posts of folks damaging the seal in theprocess of trying to hammer it in place (it is light aluminum and will distorteasily, rendering it useless). I investigated the possibility of using a smallarbor press, and after exhausting my list of contacts and neighbors, I actuallybought a cheap one from Harbor Freight. But in the process of borrowing anappropriate socket from my neighbor (a 1&1/16 impact driver socket fitperfectly), he sized it up for about 10 seconds and then said ‘you could run abolt up through the housing and probably just draw it down with a socket andwrench – just need a bolt, a couple of big washers, and a nut”.Simple and brilliant (I returned the arborpress at that point).I mounted the pumphousing on a board, after drilling a couple of holes to match the housing boltpattern, and one that lined up with the opening for the seals. I purchased a 6inch hex-head bolt (5/16th inch diameter I think) and some washersand corresponding nut. The book also calls for using Yamabond #4 as anadditional sealant on the inner surface of the housing, so I did pick up a tubeof that from the local bike shop. This is applied on the inner surface of thehousing just prior to installation of the seal. It says to use a small amount,and you also want to be careful not to plug the weep hole. It also says toapply a small amount of grease to the lip of the seal – not sure what purposethis serves, but I did as instructed.Ithen ran the bolt up through the board and the center of the pump assembly,then thought better of having threads that close to the inner wall of thehousing where the oil seal sits, so I pulled it out and put some electricaltape on that part of the threads just to make sure I did not inadvertentlyscratch the housing there. I then sat the seal in place on the housing, thesocket on top of the seal, a couple of washers and the nut and snugged it up,trying to keep the seal as straight as possible on the housing. You can’t seemuch of it at this point, but enough to make sure it is straight on. Then justa matter of slowly tightening it up – watching as it goes – but once it startsyou are pretty much committed. You will know when it is fully seated and can’tbe tightened any more. I did discover after removing the bolt and socket, thatone side had just a slight gap (enough to feel with a finger nail), so Ireinstalled the apparatus and retightened, then loosened and rotated the socketa bit and retightened, repeating this procedure until I had rotated the socketa full 360 degrees.This took care ofthe gap. At this point, visually verify that the weep hole is still clear –clean it out with a pick or maybe a pipe cleaner if necessary. The second piece of the mechanical seal is the rubber/ceramic seal thatgoes in the body of the impeller. If you are reusing the impeller, you need to removethe old seal and replace it with the new one – simply apply a little coolant tothe new seal to help lubricate it and slide it down the shaft into the body ofthe impeller. The manual says to measure that the seal fits squarely inrelation to the shaft (no tilt) – I just slipped it into place and pressed itin with my fingers - it seemed flat and flush, so hoping there is nothing moreto it than that. The next step is to install the oil seal and then the bearing. The oilseal just slips in (printed side down). The bearing needs pressed in next. Iconsidered using a narrower gauge bolt and repeating the above procedure fromthe opposite side to press in the bearing, but I was worried about the boltdamaging the inner surface of the oil seal, which the spinning shaft of theimpeller runs against. If you used a partially threaded bolt, the press methodwould probably be fine. But the bearing, being made of high quality steel, canwithstand some light hammering, so I went that route – putting a little oil onthe new bearing as a lubricant, then using the old bearing on top of the newone, with a large washer over the old bearing, and the impact socket on top ofthe washer as my hammering point. Tapping in a circular pattern around thesocket until it began to go in and just continuing until it felt seated. Itdoes not go in completely flush with the housing, but sticks out just a bit.You will know when you insert the impeller through from the other side – if theindentation for the circlip is not exposed, then the bearing is not fullyseated. At this point it is a simple matter to lube the shaft of the impellerand insert it thru the seals, install the circlip, install the dowel pin,install the gear, and the final circlip. You are now ready to install the pump back on the bike.I was replacing the L-Joint tube thatconnects to the thermostat housing, so I had a new one of those and newo-rings. If you are using the old tube, you probably at least want to replacethose o-rings. Then mount the housing back on the bike with the new gasket,then the outer housing with the new o-ring, tightening everything to spec (7.2ft/lb). Don’t forget to fill it with antifreeze before starting the bike! I have included attachments - a word doc that includes the above, and a diagram/parts list. The video that shows the assembly of the seals and bearing can be found on YouTube at this link: Hope this is some help to anyone still working on these bikes. Water-Pump-83-Venture-rebuild-narrative.docx Water-Pump-diagram-83-Venture-with-notes.pdf
- 3 replies
-
- coolant drip
- coolant leak
-
(and 3 more)
Tagged with:
-
The L-Joint as it is called was included because I asked for it - mine had a dent in the elbow and I figured it would be a lot easier to replace now than later. It is a pricey item though - about $60 list but he did give me a discount on the whole package - stll over $200. But that also included a new impeller ($77) - mine was still the original plastic one. If yours was ever replaced with an aluminum one, you shouldn't need that. I am posting my whole narrative on the rebuild, complete with video, in a new post here shortly. Hope it gives you most of the info you need.
-
Purchased a water pump rebuild kit for my 83 a while back (from Rick at Buckeye Performance) and am now getting around to install. Got everything torn down (it did still have the plastic impeller – near 80k and it was not in bad shape, but good to have the new one in hand). I have cleaned up all the surfaces and am ready to assemble the new parts. Is there a recommended sequence for installing the seals and bearing? I am thinking it would be best to install the mechanical seal (the one with the spring, on the coolant side of the assembly) first, since it is supposed to have the Yamabond4 around the inner edge. The manual shows a ‘special tool’ for pressing that piece in place– any hints for a suitable substitute? After that, then install the oil seal and bearing? Or vice-versa? Or am I over-thinking this? Any advice would be appreciated. And... I did not purchase a new thermostat - seems to be working fine - is it any more difficult to do it later if it becomes a problem?
-
83 Venture Rear Wheel Bearing Replacement (This document in Word format attached)[ATTACH]106806[/ATTACH]. My apologies for the formatting below - outlines don't come out very well in plain text. See the Word doc. I was experiencing some rear noise and vibration when leaning to the left and it was becoming progressively worse. I had never done the ‘Venture Rear Wheel Service” as documented in the forum (Ozlander 09-17-2015), so I decided to undertake that. I took the original write-up, and broke it down into numbered steps so I could check each one off as I went (I just find that a little easier to follow). I have included that below. I did not find any problems until I came to the bearing inspection part of the process, I did notice a little bit of roughness in the gear-side bearing (the needle bearing), but even more unusual, there was significant play in the inner bearing collar that forms the inner race of that bearing (it would slide in and out about 3/8’s of an inch). So I decided to undertake a replacement of the entire set. I searched the forums high and low for information on how to do that, and found a number of them, but there are differences between the different generations (to be expected), and there may be differences between the 3 years of the first gens. I can only speak about my experiences with this 83. After reviewing the various forums, I began the process of ordering the parts. Here is the complete list of parts as extracted from the YAMAHA parts website (https://www.shopyamaha.com/parts-catalog/parts/star-mcy?ls=Star&dealernumber=#/Yamaha/XVZ12TK_-_1983/REAR_WHEEL ) 1983 XVZ12TK & TDK per Yamaha's web site Item # Part # Description Yamaha price 3 93317-32635-00 BEARING, CYLINDRICAL | Use w/Item 28 38.78 kit 2 90560-20235-00 Spacer 19.37 4 90387-200J2-00 COLLAR 14.22 5 93306-30417-00 BEARING 32.18 kit replaced by part # 93306-30437-00 6 99009-52500-00 CIRCLIP 6.41 7 93102-25064-00 OIL SEAL 7.64 kit 12 93440-45022-00 CIRCLIP 6.67 13 93210-68347-00 O-RING 4.72 kit 14 2H7-25315-00-00 FLANGE, SPACER 5.5 partzilla 15 93106-40027-00 OIL SEAL 8.27 kit 28 90387-203H7-00 COLLAR | Use w/Item #3 15.41 partzilla Total $ 159.17 Don’t let the Yamaha price scare you, as you can’t order any of this from them anyway. I listed it just for reference purposes as I shopped around. I found a reference in one of the forums to a kit from OEMCYCLE (Pivot Works part # PWRWS-Y23-000) and it was available for $55 so I ordered it. The only drawback was that they did not list the detail parts that were included in the kit. So I waited until it arrived to find out exactly what was in it – those are noted in the list above by ‘kit’ - it was missing two critical parts – Item 14 (FLANGE,SPACER), and Item 28 (COLLAR). The name for Item 28 is a bit of a misnomer as it is actually the inner piece of the needle bearing that functions as the inner race for that bearing (and is the piece that I noted above was moving in and out suspiciously) – the YAMAHA site specifically states that it should be ordered in conjunction with Item 3 (the outer portion of the needle bearing). OEMCYCLE did not list that part as orderable (nor did the Pivot Works site either), so I was able to find it on Partzilla (along with the SPACER FLANGE – more about that below). The parts I did not order and reused were the two circlips, the SPACER (Item 2), and Item 4 (COLLAR) which is more of a washer that is external to the bearings and seals. I should note at this point, that in my original Service Manual for the 83, the Rear Wheel Diagram (Page 5-7) does not show Item # 28 (the COLLAR that forms the inner race for the bearing) – it is present on the Yamaha Website diagram – I have now penciled it in on my manual. REMOVING THE OLD BEARINGS: I searched the forums for some details on this, and was not confident that what I found would actually pertain to the 83. I was able to find a webpage (by searching for the bearing part numbers) which documented bearing removal for an XS11 and looked exactly the same as what I was seeing on the 83 Venture. It was good up to a certain point, but then deviated from the reality of the 83 as I will note below. So here is the link – good pix and text – I will summarize the steps my buddy (Tim Tucker) and I actually took and where we had to deviate from the XS11 procedure. Link to pix from XS11 Yamaha – had same part # for one of the bearings: http://www.xs11.com/xs11-info/tech-tips/repairs/32/193-rear-wheel-bearing-replacement-pictorial.html 1. Starting on the brake side, we used a seal puller to remove the oil seal, exposing the circlip underneath. 2. We removed the circlip, so the bearing could now be pounded out from the opposite side (in theory, once you have that side opened up). 3. We turned the tire over (setting it on a pair of wood 2x4’s to protect the brake disc) and tried to follow the step in the XS11 procedure – it shows using a seal puller to remove the seal and collar – that does not work for the 83 – the seal and collar are a different part. The seal on the 83 is rubber/vinyl with an external metal ring (that is pressed into the hub) but more importantly, it contains a tiny embedded coil spring – the spring is what prevents the collar from pulling completely out of the bearing. We ended up cutting the outer rubber portion of the seal all the way around until we exposed the spring, then pulled that out with a pair of needle nose pliers. That allowed the inner collar to slide completely out. With the extra room, we were then able to grab the rest of the seal with a pair of diagonals, distort it, and twist it completely out. So what you are left with at this point on the gear side is the outer race and needle bearings. 4. The XS11 procedure now states to hammer out the big bearing from this side, by shifting the flanged spacer over, to gain access to the outer race of the big bearing. This is an oversimplification of what needs to happen (for the 83 at least) and is a good time to describe what is actually in this hub and how it is meant to fit together. The design is that the long Spacer aligns with the inner race of the large bearing and with the inner race (the ‘collar’ noted above) of the needle bearing so that those parts remain relatively stationary while the wheel itself rotates with the outer races. The Spacer Flange is there to maintain the proper alignment of the long Spacer with the center of the large bearing – because the cavity at that end of the wheel hub is the diameter of the large bearing, so there is all that space for the long spacer to flop around. The Spacer Flange is basically a donut that is the same diameter as the large bearing, and the long spacer fits inside the donut hole, lining up with the inner race. At this point in the removal, we did not understand that. We could not get the spacer to ‘shift’ as the XS11 procedure stated – it would wiggle very slightly, to reveal the edge of the inner race, but no more. We eventually resorted to hammering on the spacer with a large drift pin, which basically distorted the Spacer Flange until the long spacer came loose from the center of the Spacer Flange and was then free to slide all around the inside cavity of the hub, revealing the outer race of the large bearing and making that accessible to hammering with the drift pin. Of course the Spacer Flange was sitting on top of the large bearing, but being thin metal, it was perfectly fine to hammer on it to pound out the large bearing. Once that popped out, the mangled Spacer Flange came with it, and the long Spacer fell out as well. Knowing what we know now, we suspect that it would have been possible from the needle bearing side to pull the Spacer/SpacerFlange assembly up thru the needle bearing (the Spacer is the same diameter as the needle bearing collar we removed above) just enough so that the Flange portion would clear the housing above the large bearing – it might pivot just enough to get a drift pin down thru the spacers and catch the outer race of the large bearing, allowing you to hammer it out – the next person to follow this procedure will need to update this document with their findings. 5. That left just the needle bearing still in the wheel on the gear side. The XS11 procedure had a picture showing two cutouts in the inner wheel housing that would allow you to insert a small drift pin to hammer out the needle bearing from the opposite side. Unfortunately, there were no cutouts on the 83’s hub. The hub completely blocks any access to the bearing from the opposite side. I considered drilling my own holes, but eventually decided against that. So at this point I cried uncle, and took the wheel to a local bike shop. For a half-hour labor’s charge, they told me that they ripped out the needle bearings form the outer race, then used a small bearing puller that budged it enough so the inside edge of the bearing was then exposed enough to catch it with a drift pin from the other side, and finished by hammering it out. 6. Installing the new bearings: we laid out the parts and slid them onto the axle to verify we understood how it needed to go back together. Started with the large sealed bearing, then the Spacer Flange (open side against the bearing, followed by the long Spacer, then the Collar (Inner Race of the needle bearing) and then the needle bearing itself (which we had not yet greased up and so we did not actually slide the collar into it). This is the point where we first really understood how it all was meant to work. When we initially slid the Spacer Flange up against the large bearing, it was contacting the bearing’s rubber seal and wanted to turn with the outer race. We knew that couldn’t be right, and it finally dawned on us that the long Spacer was meant to fit through the Spacer Flange and thus keep the flange from contacting the rubber seal. a. So the next step was to insert the long Spacer into the Spacer Flange. This is accomplished simply by laying the Spacer Flange on a flat surface (open side down) and tapping the long spacer through the center until it comes into contact with the flat surface. The end result is the long Spacer protrudes thru the flange to allow it to contact the bearing while preventing the outer edge of the Flange Spacer from touching the bearing seal or outer race. We verified that by sliding everything back onto the axle and now the only parts touching were those that lined up with the inner race of both bearings. b. Lay the wheel with the large bearing side up c. Insert the Spacer/Flange Spacer assembly into the hub (long spacer first – it will protrude out the other side of the hub). d. Insert the new large bearing into the hub and gently hammer into place. We used the tip from the XS11 instructions and had already cut a notch out of the old bearing, so we laid the old bearing on top of the new one and hammered on that until the new one was completely seated. The old bearing pops right out of the wheel housing when squeezed with a pair of plyers. e. Install the circlip f. Install the new seal g. Flip the wheel over – the Spacer/Flange Spacer assembly should slip back down and sit on the newly installed bearing h. Grease the new needle bearing i. Install new needle bearing – again we used the old needle bearing (which we also had notched) as a hammering tool. j. Apply a little grease to the new Collar (inner race) and insert into the needle bearing (smaller end first). It should butt against the Spacer inside the hub. k. Install the oil seal l. Reinstall the hub per the instructions in the Rear Wheel Service document i. Apply grease to the inside of the hub and to the six posts that fit into the wheel. ii. Check the o-ring on the wheel to be sure it is in place before you replace the hub and circlip. 7. The wheel is now ready for installation. Venture Rear Wheel Service You may ask, "Doesn't my dealer do that?" NOT UNLESS YOU TELL, HIM THAT YOU WANT IT DONE. This service should be completed every tire change or 10,000 miles (16,000k) or at least every two years; but in most cases it isn't done because we don't always have a dealer replace our tires and/or we don't tell him to do the work. So if you just bought the bike or you are not sure it has been done, it would be a good time to think about servicing the rear wheel of your Venture. The procedure is fairly simple to do on bikes without a trailer hitch and only a little harder if your bike has one. 1. Remove the rear bags 2. Remove the right muffler 3. Remove the rear brake caliper 4. Deflate the tire; then remove the rear wheel: a. Remove the axel cotter pin, washer, and axel nut b. Remove the caliper and loosen the pinch bolt c. While supporting the brake torque stopper plate, pull out the rear axel d. Move the wheel to the right side and separate it from the final gear cases and remove the rear wheel. 5. If your Venture is a 1983, 84, or 85 you will need to remove the rear drive or differential and remove the drive shaft: a. Remove the final gear case assembly b. Remove the drive shaft. 6. Clean the drive shaft and coupling, then grease both ends before putting it back in (note: make sure that the shaft goes back into the u-joint. If you are not sure, remove the spring on the boot covering the u-joint and check it. Next clean the spline or gear on the rear drive and grease it with a good quality grease, personally I use a medium Moly based grease. 7. Wheel cleaning/inspection: a. Now find a couple of 2" x 4"s and place the rear wheel (spline side up) on the boards. b. When you clean the hub and splines off you will see the spring clip or circlip that holds the hub in place; i. remove this clip and before you remove the hub mark the position of the hub so you can replace it in the same holes it came from. ii. Now clean the hub and inspect it for wear iii. Then apply grease to the inside of the hub and to the six posts that fit into the wheel. iv. Check the o-ring on the wheel to be sure it is in place before you replace the hub and circlip. v. Check the bearings inside of the wheel and check the bearing movement; if they are rough or worn replace them. 8. Now for the mono shock pivots: a. Place a jack under the rear drive to take the strain off of the mono shock then dissemble. b. Clean and grease all of the pivot points and reassemble (if you have a 90 - 93 or you have had grease fittings installed, just give them a squirt). 9. Before you install the rear wheel take the axle and put it back through the swing arm into the final drive to check the alignment. If you find that it is in a bind you will have to change the wedge shim between the final drive and the swing arm. 10. Check the oil level in the rear drive or replace the oil if it has been 10,000 miles since it was serviced and check the brake pads for wear. 11. You can now reassemble your bike and have another year or two of trouble free riding. 83 Venture-Rear-Wheel-Bearings-Replacement.docx
-
83 Venture Rear Wheel Bearing Replacement (This document in Word format attached)83 Venture-Rear-Wheel-Bearings-Replacement.docx. My apologies for the formatting below - outlines don't come out very well in plain text. See the Word doc. I was experiencing some rear noise and vibration when leaning to the left and it was becoming progressively worse. I had never done the ‘Venture Rear Wheel Service” as documented in the forum (Ozlander 09-17-2015), so I decided to undertake that. I took the original write-up, and broke it down into numbered steps so I could check each one off as I went (I just find that a little easier to follow). I have included that below. I did not find any problems until I came to the bearing inspection part of the process, I did notice a little bit of roughness in the gear-side bearing (the needle bearing), but even more unusual, there was significant play in the inner bearing collar that forms the inner race of that bearing (it would slide in and out about 3/8’s of an inch). So I decided to undertake a replacement of the entire set. I searched the forums high and low for information on how to do that, and found a number of them, but there are differences between the different generations (to be expected), and there may be differences between the 3 years of the first gens. I can only speak about my experiences with this 83. After reviewing the various forums, I began the process of ordering the parts. Here is the complete list of parts as extracted from the YAMAHA parts website (https://www.shopyamaha.com/parts-catalog/parts/star-mcy?ls=Star&dealernumber=#/Yamaha/XVZ12TK_-_1983/REAR_WHEEL ) 1983 XVZ12TK & TDK per Yamaha's web site Item # Part # Description Yamaha price 3 93317-32635-00 BEARING, CYLINDRICAL | Use w/Item 28 38.78 kit 2 90560-20235-00 Spacer 19.37 4 90387-200J2-00 COLLAR 14.22 5 93306-30417-00 BEARING 32.18 kit replaced by part # 93306-30437-00 6 99009-52500-00 CIRCLIP 6.41 7 93102-25064-00 OIL SEAL 7.64 kit 12 93440-45022-00 CIRCLIP 6.67 13 93210-68347-00 O-RING 4.72 kit 14 2H7-25315-00-00 FLANGE, SPACER 5.5 partzilla 15 93106-40027-00 OIL SEAL 8.27 kit 28 90387-203H7-00 COLLAR | Use w/Item #3 15.41 partzilla Total $ 159.17 Don’t let the Yamaha price scare you, as you can’t order any of this from them anyway. I listed it just for reference purposes as I shopped around. I found a reference in one of the forums to a kit from OEMCYCLE (Pivot Works part # PWRWS-Y23-000) and it was available for $55 so I ordered it. The only drawback was that they did not list the detail parts that were included in the kit. So I waited until it arrived to find out exactly what was in it – those are noted in the list above by ‘kit’ - it was missing two critical parts – Item 14 (FLANGE,SPACER), and Item 28 (COLLAR). The name for Item 28 is a bit of a misnomer as it is actually the inner piece of the needle bearing that functions as the inner race for that bearing (and is the piece that I noted above was moving in and out suspiciously) – the YAMAHA site specifically states that it should be ordered in conjunction with Item 3 (the outer portion of the needle bearing). OEMCYCLE did not list that part as orderable (nor did the Pivot Works site either), so I was able to find it on Partzilla (along with the SPACER FLANGE – more about that below). The parts I did not order and reused were the two circlips, the SPACER (Item 2), and Item 4 (COLLAR) which is more of a washer that is external to the bearings and seals. I should note at this point, that in my original Service Manual for the 83, the Rear Wheel Diagram (Page 5-7) does not show Item # 28 (the COLLAR that forms the inner race for the bearing) – it is present on the Yamaha Website diagram – I have now penciled it in on my manual. REMOVING THE OLD BEARINGS: I searched the forums for some details on this, and was not confident that what I found would actually pertain to the 83. I was able to find a webpage (by searching for the bearing part numbers) which documented bearing removal for an XS11 and looked exactly the same as what I was seeing on the 83 Venture. It was good up to a certain point, but then deviated from the reality of the 83 as I will note below. So here is the link – good pix and text – I will summarize the steps my buddy (Tim Tucker) and I actually took and where we had to deviate from the XS11 procedure. Link to pix from XS11 Yamaha – had same part # for one of the bearings: http://www.xs11.com/xs11-info/tech-tips/repairs/32/193-rear-wheel-bearing-replacement-pictorial.html 1. Starting on the brake side, we used a seal puller to remove the oil seal, exposing the circlip underneath. 2. We removed the circlip, so the bearing could now be pounded out from the opposite side (in theory, once you have that side opened up). 3. We turned the tire over (setting it on a pair of wood 2x4’s to protect the brake disc) and tried to follow the step in the XS11 procedure – it shows using a seal puller to remove the seal and collar – that does not work for the 83 – the seal and collar are a different part. The seal on the 83 is rubber/vinyl with an external metal ring (that is pressed into the hub) but more importantly, it contains a tiny embedded coil spring – the spring is what prevents the collar from pulling completely out of the bearing. We ended up cutting the outer rubber portion of the seal all the way around until we exposed the spring, then pulled that out with a pair of needle nose pliers. That allowed the inner collar to slide completely out. With the extra room, we were then able to grab the rest of the seal with a pair of diagonals, distort it, and twist it completely out. So what you are left with at this point on the gear side is the outer race and needle bearings. 4. The XS11 procedure now states to hammer out the big bearing from this side, by shifting the flanged spacer over, to gain access to the outer race of the big bearing. This is an oversimplification of what needs to happen (for the 83 at least) and is a good time to describe what is actually in this hub and how it is meant to fit together. The design is that the long Spacer aligns with the inner race of the large bearing and with the inner race (the ‘collar’ noted above) of the needle bearing so that those parts remain relatively stationary while the wheel itself rotates with the outer races. The Spacer Flange is there to maintain the proper alignment of the long Spacer with the center of the large bearing – because the cavity at that end of the wheel hub is the diameter of the large bearing, so there is all that space for the long spacer to flop around. The Spacer Flange is basically a donut that is the same diameter as the large bearing, and the long spacer fits inside the donut hole, lining up with the inner race. At this point in the removal, we did not understand that. We could not get the spacer to ‘shift’ as the XS11 procedure stated – it would wiggle very slightly, to reveal the edge of the inner race, but no more. We eventually resorted to hammering on the spacer with a large drift pin, which basically distorted the Spacer Flange until the long spacer came loose from the center of the Spacer Flange and was then free to slide all around the inside cavity of the hub, revealing the outer race of the large bearing and making that accessible to hammering with the drift pin. Of course the Spacer Flange was sitting on top of the large bearing, but being thin metal, it was perfectly fine to hammer on it to pound out the large bearing. Once that popped out, the mangled Spacer Flange came with it, and the long Spacer fell out as well. Knowing what we know now, we suspect that it would have been possible from the needle bearing side to pull the Spacer/SpacerFlange assembly up thru the needle bearing (the Spacer is the same diameter as the needle bearing collar we removed above) just enough so that the Flange portion would clear the housing above the large bearing – it might pivot just enough to get a drift pin down thru the spacers and catch the outer race of the large bearing, allowing you to hammer it out – the next person to follow this procedure will need to update this document with their findings. 5. That left just the needle bearing still in the wheel on the gear side. The XS11 procedure had a picture showing two cutouts in the inner wheel housing that would allow you to insert a small drift pin to hammer out the needle bearing from the opposite side. Unfortunately, there were no cutouts on the 83’s hub. The hub completely blocks any access to the bearing from the opposite side. I considered drilling my own holes, but eventually decided against that. So at this point I cried uncle, and took the wheel to a local bike shop. For a half-hour labor’s charge, they told me that they ripped out the needle bearings form the outer race, then used a small bearing puller that budged it enough so the inside edge of the bearing was then exposed enough to catch it with a drift pin from the other side, and finished by hammering it out. 6. Installing the new bearings: we laid out the parts and slid them onto the axle to verify we understood how it needed to go back together. Started with the large sealed bearing, then the Spacer Flange (open side against the bearing, followed by the long Spacer, then the Collar (Inner Race of the needle bearing) and then the needle bearing itself (which we had not yet greased up and so we did not actually slide the collar into it). This is the point where we first really understood how it all was meant to work. When we initially slid the Spacer Flange up against the large bearing, it was contacting the bearing’s rubber seal and wanted to turn with the outer race. We knew that couldn’t be right, and it finally dawned on us that the long Spacer was meant to fit through the Spacer Flange and thus keep the flange from contacting the rubber seal. a. So the next step was to insert the long Spacer into the Spacer Flange. This is accomplished simply by laying the Spacer Flange on a flat surface (open side down) and tapping the long spacer through the center until it comes into contact with the flat surface. The end result is the long Spacer protrudes thru the flange to allow it to contact the bearing while preventing the outer edge of the Flange Spacer from touching the bearing seal or outer race. We verified that by sliding everything back onto the axle and now the only parts touching were those that lined up with the inner race of both bearings. b. Lay the wheel with the large bearing side up c. Insert the Spacer/Flange Spacer assembly into the hub (long spacer first – it will protrude out the other side of the hub). d. Insert the new large bearing into the hub and gently hammer into place. We used the tip from the XS11 instructions and had already cut a notch out of the old bearing, so we laid the old bearing on top of the new one and hammered on that until the new one was completely seated. The old bearing pops right out of the wheel housing when squeezed with a pair of plyers. e. Install the circlip f. Install the new seal g. Flip the wheel over – the Spacer/Flange Spacer assembly should slip back down and sit on the newly installed bearing h. Grease the new needle bearing i. Install new needle bearing – again we used the old needle bearing (which we also had notched) as a hammering tool. j. Apply a little grease to the new Collar (inner race) and insert into the needle bearing (smaller end first). It should butt against the Spacer inside the hub. k. Install the oil seal l. Reinstall the hub per the instructions in the Rear Wheel Service document i. Apply grease to the inside of the hub and to the six posts that fit into the wheel. ii. Check the o-ring on the wheel to be sure it is in place before you replace the hub and circlip. 7. The wheel is now ready for installation. Venture Rear Wheel Service You may ask, "Doesn't my dealer do that?" NOT UNLESS YOU TELL, HIM THAT YOU WANT IT DONE. This service should be completed every tire change or 10,000 miles (16,000k) or at least every two years; but in most cases it isn't done because we don't always have a dealer replace our tires and/or we don't tell him to do the work. So if you just bought the bike or you are not sure it has been done, it would be a good time to think about servicing the rear wheel of your Venture. The procedure is fairly simple to do on bikes without a trailer hitch and only a little harder if your bike has one. 1. Remove the rear bags 2. Remove the right muffler 3. Remove the rear brake caliper 4. Deflate the tire; then remove the rear wheel: a. Remove the axel cotter pin, washer, and axel nut b. Remove the caliper and loosen the pinch bolt c. While supporting the brake torque stopper plate, pull out the rear axel d. Move the wheel to the right side and separate it from the final gear cases and remove the rear wheel. 5. If your Venture is a 1983, 84, or 85 you will need to remove the rear drive or differential and remove the drive shaft: a. Remove the final gear case assembly b. Remove the drive shaft. 6. Clean the drive shaft and coupling, then grease both ends before putting it back in (note: make sure that the shaft goes back into the u-joint. If you are not sure, remove the spring on the boot covering the u-joint and check it. Next clean the spline or gear on the rear drive and grease it with a good quality grease, personally I use a medium Moly based grease. 7. Wheel cleaning/inspection: a. Now find a couple of 2" x 4"s and place the rear wheel (spline side up) on the boards. b. When you clean the hub and splines off you will see the spring clip or circlip that holds the hub in place; i. remove this clip and before you remove the hub mark the position of the hub so you can replace it in the same holes it came from. ii. Now clean the hub and inspect it for wear iii. Then apply grease to the inside of the hub and to the six posts that fit into the wheel. iv. Check the o-ring on the wheel to be sure it is in place before you replace the hub and circlip. v. Check the bearings inside of the wheel and check the bearing movement; if they are rough or worn replace them. 8. Now for the mono shock pivots: a. Place a jack under the rear drive to take the strain off of the mono shock then dissemble. b. Clean and grease all of the pivot points and reassemble (if you have a 90 - 93 or you have had grease fittings installed, just give them a squirt). 9. Before you install the rear wheel take the axle and put it back through the swing arm into the final drive to check the alignment. If you find that it is in a bind you will have to change the wedge shim between the final drive and the swing arm. 10. Check the oil level in the rear drive or replace the oil if it has been 10,000 miles since it was serviced and check the brake pads for wear. 11. You can now reassemble your bike and have another year or two of trouble free riding.